
CS
EDM2000 is an easy-to use program oriented to serve wire EDM Machines on four axes.
The
interpretation of more common CAD formats like MI, DXF, IGES 2D, IGES
3D, STEP enables the quick bridge from the mechanical drawing to the
CNC File for machining.
The geometric window
displies the loaded files and enables the commands to modify and
optimize the drawing, the geometric window is also enabled to define
independent geometry from the CAD.
Read 3D files from all solid modeller (Es.: Rhino)
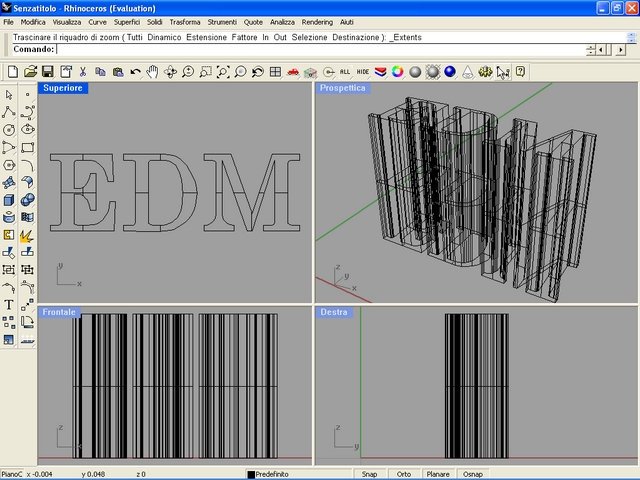 | Implementation with ESPRIT ( VB MACRO )
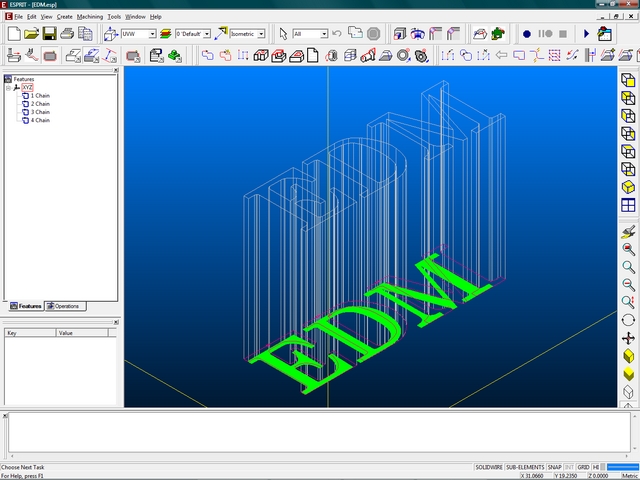 | Cut 3D file with Automatic FIX
 | Automatic Profiles Identification
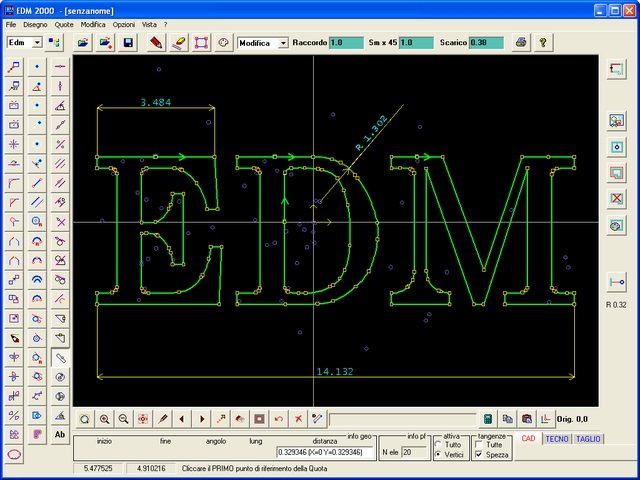 | Customized Technological DATABASE
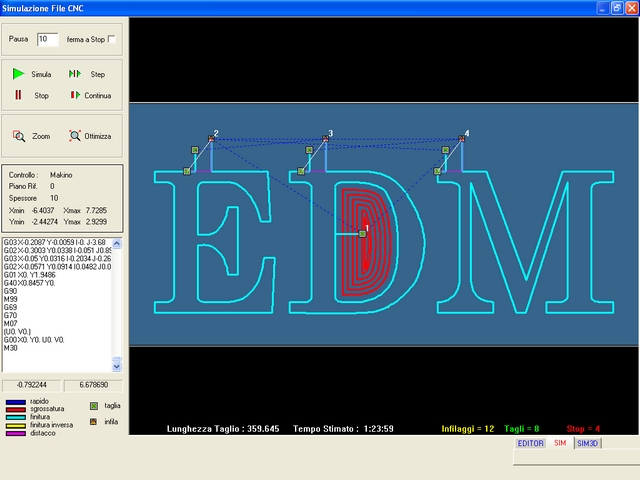 | Simulation
of the CNC File
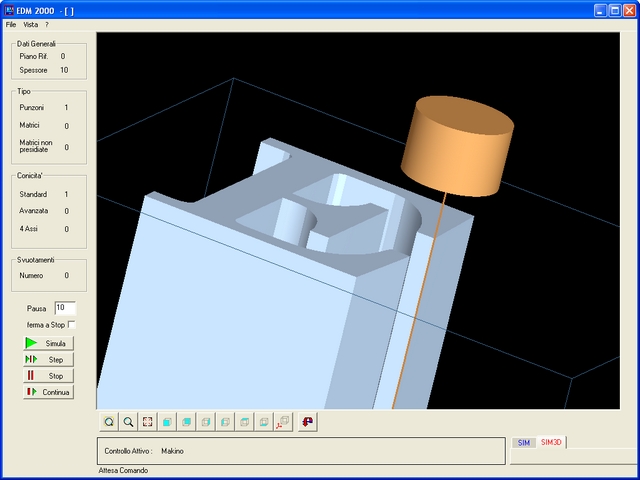 |
Passing and vertical hole identification
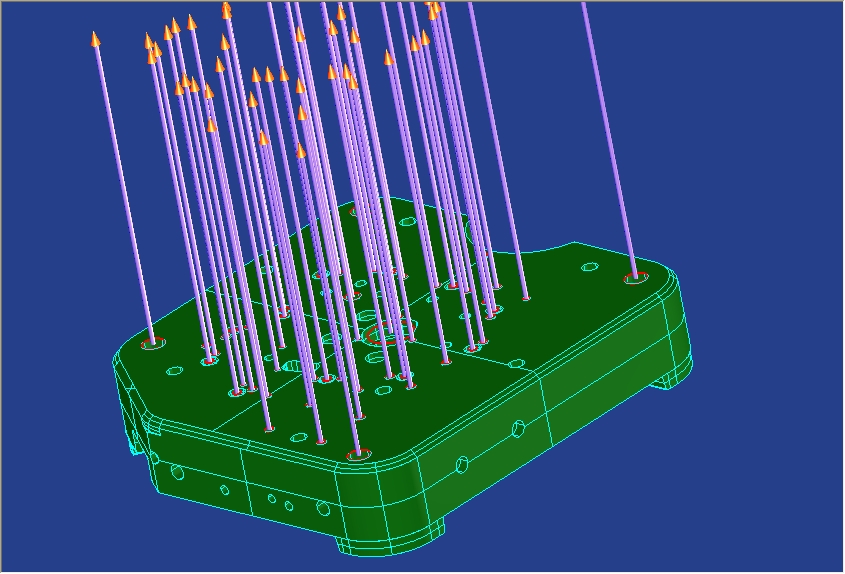 | Electrodes positions and orientation data
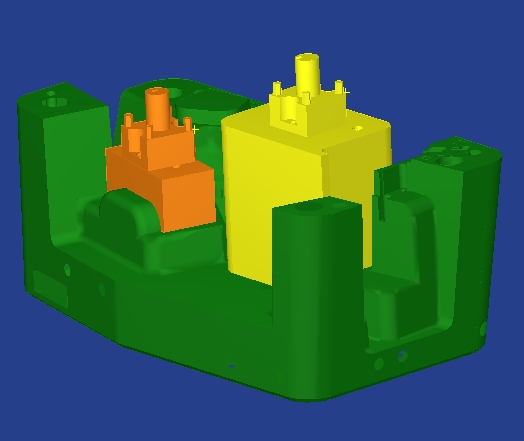 |
Iso file of electrodes data for more EDM machines
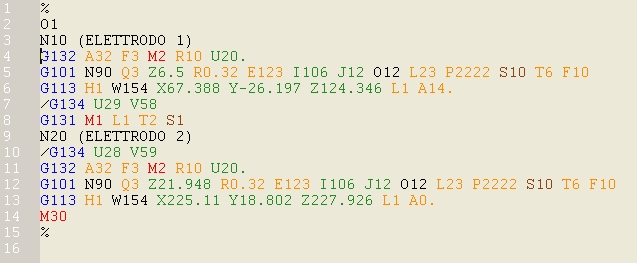
|
Benefits :
- Simultaneus data INPUT and Check of DATA.
- Complete graphic representation of the job with drastic reduction of errors.
- Quick transition among the Geometry and Technology windows to editing : every modify acts immediatly on the CNC File.
- Availability of a specially created Editor, on line, for a quick and safe setup of the CNC File.
- Graphic simulation of the CNC File and CNC Dry-Run simulation (2D & 3D).
- Availability of many and updated customized Post-processor and technological Data-Base.
- Verify of Wire Draving Head path
The
geometric window displies the loaded files and enables the commands to
modify and optimize the drawing, the geometric window is also enabled
to define independent geometry from the CAD :
- Positioning of the Zero Working (also for a lot of Parts Simultaneously Loaded).
- Clearing of unnecessary Geometry and management of the Active Colours.
- Repetitions with POSITIONING and ROTATION.
- Introduction
of NEW GEOMETRY ( IE : FILLETS, POINTS, SEGMENTS, ARCS AND SO ON ) and
definition of new PROFILES NOT ACQUIRED FROM CAD.
- Correction of TANGENCY PROBLEMS using the commands TRIM, CUT, EXTEND.
- IMMEDIATE AUTOMATIC GENERATION OF CANONICS PROFILES (Slots, Polygons, and so on).
- AUTOMATIC PROFILES IDENTIFICATION.
- PARAMETRIC INSERTION OF UNDERCUT IN THE SELECTED EDGES.
- AUTOMATIC
GENERATION OF PROFILES FROM 3D SURFACES CUTTING OPTION : IGES3D-CUT
enables the cut of 3D-surfaces, on paralel working planes directly from
IGES 3D Files, to generate bidimensional profiles to obtain ROLLED
SURFACES (3D SOLID) USING FOUR AXES.
Availables Modules : | Base | 2D
Drawing, n.1 Post-Processor, Work strategy management, Avanced
tapering, 4 Axes management, Closed profiles poketing, Reading Files
DXF – IGES – MI – ISO Std., Generated CN File Simulation, Editor
On-Line of CN File, Rendering visualisation of the obtained workpiece. | Optional | Reading
Files IGES 3D, Cut on three work plane, Rendering and wireframe
visualisation of the solid, Managing of the Zero position and
inclination of the workpiece in respect to the reference Axes,
informations about outside dimensions, vertex position, edges and faces
recognition, Image manipulation. | Optional | Automatic Tacking-Up of not worked paths (MAKINO only) | Optional | Technological Data-Base | Optional | Set of Post-Processors : AGIE AGIEVISION CHARMILLES FANUC MAKINO MITSUBISHI ONA SODICK SIELT | Optional | Multiple Data Transfering on Serial Line. |
 |